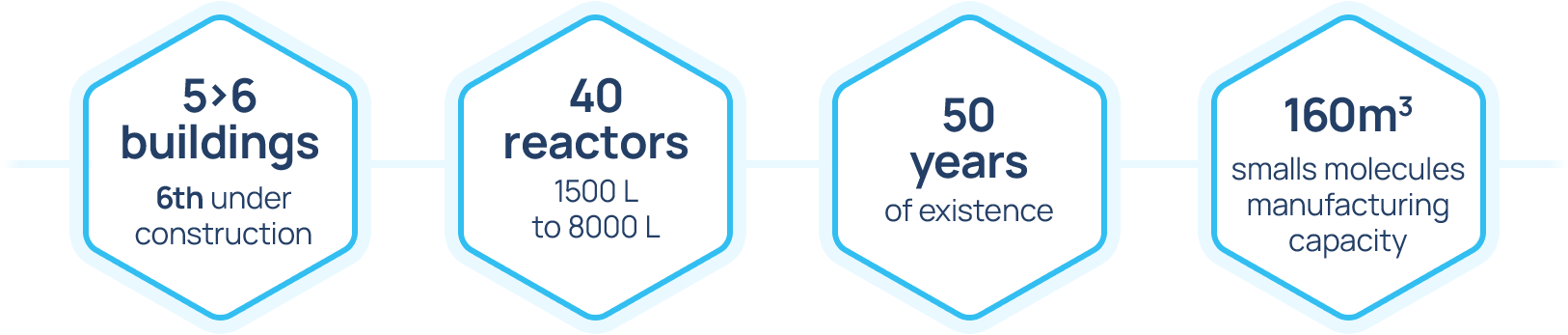
INTEROR can therefore take part in significant industrial development projects related to its area of expertise.

Capabilities
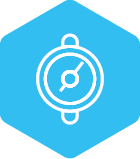
High and low pressure
High pressure :
4 vessels, max 120 bars, 300°C
Medium pressure :
1 hydrogenator 2,5m3 (loop) stainless
steel 40 bars, 160°C
1 hydrogenator 2,5m3 (vertical reactor)
12 bars, 160°C
Low pressure :
1 reactor 3 m3, 5 bars, 160°C
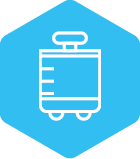
38 reactors
26 Glass lined, 12 stainless steel
reactors
From 1.5m3 to 8m3, mainly 3m3 and 6m3
Up to 300°C oil heat, 180°C steam heat
Pressure up to 3 bars
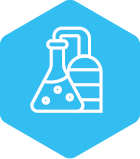
Distillation
1 dedicated building : colmun with max
12 plates, 4m3 glass lined distillator.
High temperature up to 160°C, pressure
3 mbars
1 Short Path distillator
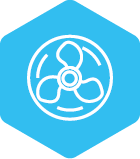
15 dryer filters, centrifuges
7 centifuges
1 agitated Nutsche Filter
7 dryers (4 biconical rotary vaccum dryers,
2 paddle dryers and 1 Guedu Pan dryer)
2 drying buildings with one ISO 8 room
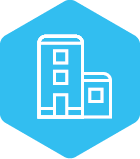
Dunopale (New building)
5 glass lined reactors and 1 stainless steel reactor from 4m3 to 10m3
1 agitated Nutsche Filtrer-Dryer
-
MANUFACTURER SPECIALIZING IN FINE CHEMICALS
INTEROR’s dedicated state-of-the-art cGMP manufacturing facilities support the small molecules contract manufacturing business.
-
LARGE-SCALE MANUFACTURING
Large volumes can be produced according to customer needs, without requiring the clients to invest in expensive production facilities.
- Capacity of 160 m3 with 5 buildings. The 6th building is under construction.
- 40 reactors from (70L) 1500 L to 8000 L.
- Scale-up from kilograms to several tons
- Batch process
- Isolation and drying devices
-
ADAPTIVE CAPACITY
Interor can adjust production quantities according to customer requirement, allowing more flexible management of demand and seasonality.
-
OPTIMISATION
INTEROR offers its capacity of development and OPTIMISATION ON CUSTOM MANUFACTURING BASIS UNDER STRICT CONFIDENTIALITY.
Improving manufacturing processes : optimize manufacturing techniques and offer more environmentally friendly and cost-effective solutions.
Cost reduction : Thanks to his expertise, help to reduce production costs while maintaining or improving product quality.
Access to advanced technologies : implement cutting-edge technologies that the client would not necessarily have in-house, such as automated systems or advanced chemical synthesis methods.
-
COMPLIANCE & RISK MANAGEMENT
Compliance with standards and regulations is crucial, especially in the chemical, pharmaceutical and cosmetic sectors. INTEROR is able to :
Ensure regulatory compliance :
INTEROR is familiar with local and international standards (REACH, CLP, FDA, etc.) and ensures that finished products comply with all applicable regulations.Managing product risks : expertise on risk management, including the management of health and environmental hazards, as well as safety in production.
Carry out routine quality control production by our engineers and well trained technicians.
-
POST-PRODUCTION
INTEROR offers logistics services that simplify the supply chain. Interor can also support its clients' marketing & technicals efforts.
Inventory Management : manage inventories of raw materials and finished products, ensuring constant availability for the customer.
Certifications and Claims : tips for obtaining relevant certifications that can be used in marketing communications, such as ecological or quality certifications.
Technical Support and After-Sales Service : once the product is launched = ongoing technical support to resolve performance or quality issues and assistance in managing relationships with end customers.
Core Technologies
Apart the hydrogenation workshop dedicated to hydrogenation and pressure reactions, each building has been designed to handle specific hazardous chemistry but remains truly multi-purpose allowing classical chemistry to be run for multi-steps synthesis.
Core technologies for custom manufacturing / exclusive synthesis
![]() |
![]() |
![]() |
![]() |
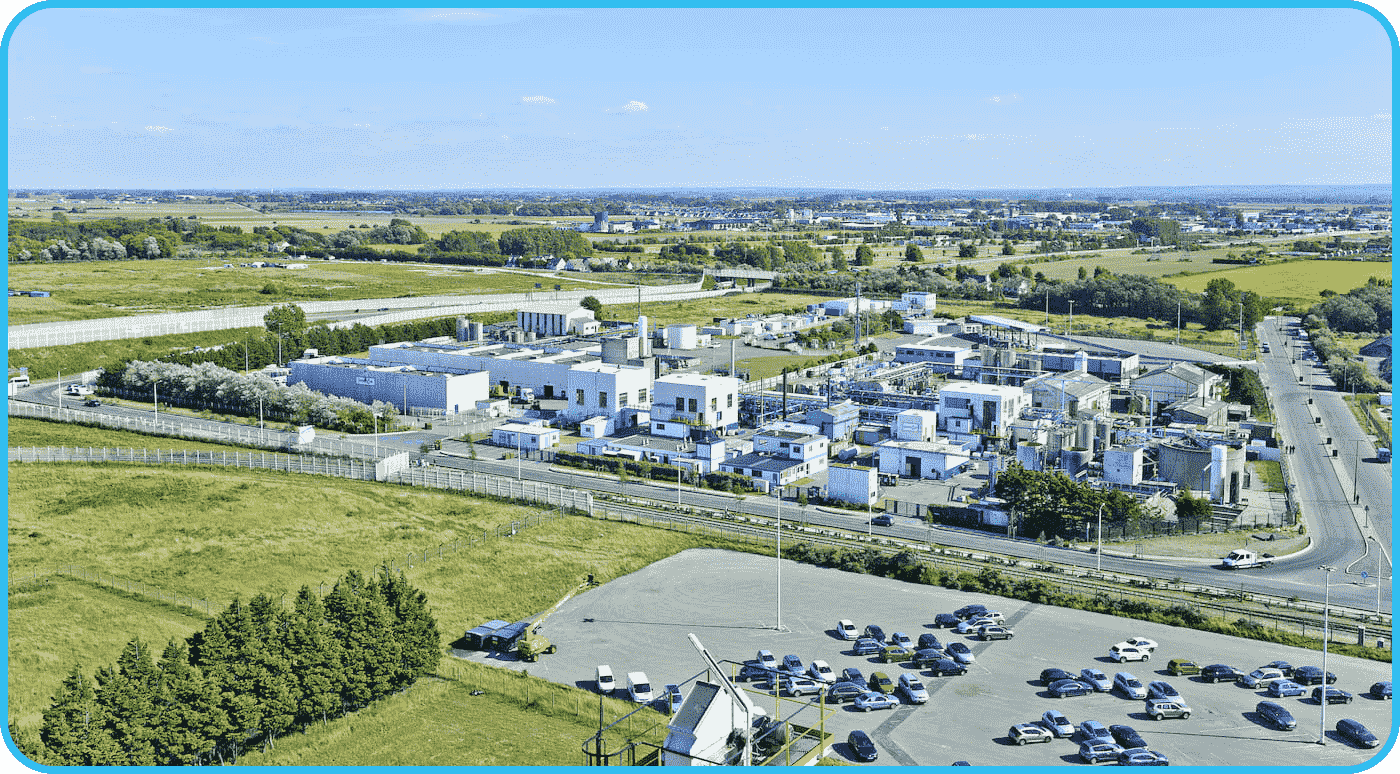