Reliable partner in the chemicals
Interor is a CRO - CDMO specializing in fine chemicals, particularly in the field of advanced organic intermediates for the pharmaceutical industry, cosmetics and specialty chemicals.
Partner today
Our business segments include :
- Custom Manufacturing
- Advanced Intermediates
- Ingredients
- Specialty Chemicals
Partner for the future
Our partnership include :
- Research & development
- Quality drug substances
- Operational excellence
- Sustainability for a better world
3 core industries
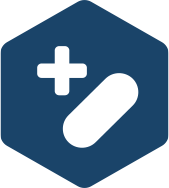
Pharmaceutical
Industry
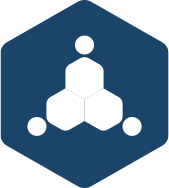
Speciality
Chemicals
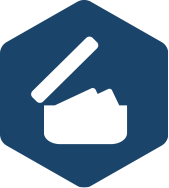
Cosmetics
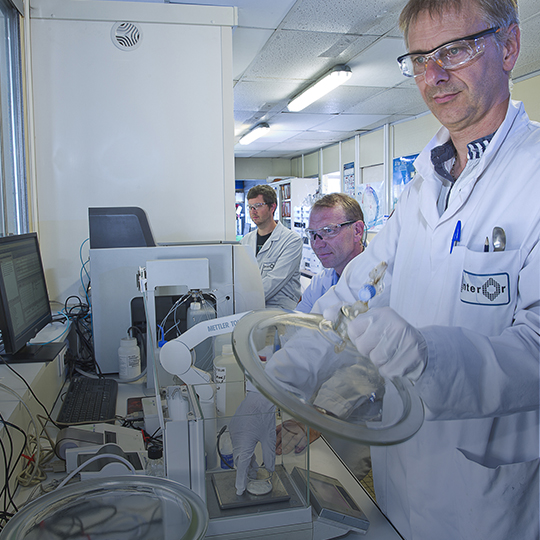
Development
Development
- Research
- Process development services
- QA & Regulatory Analytical support
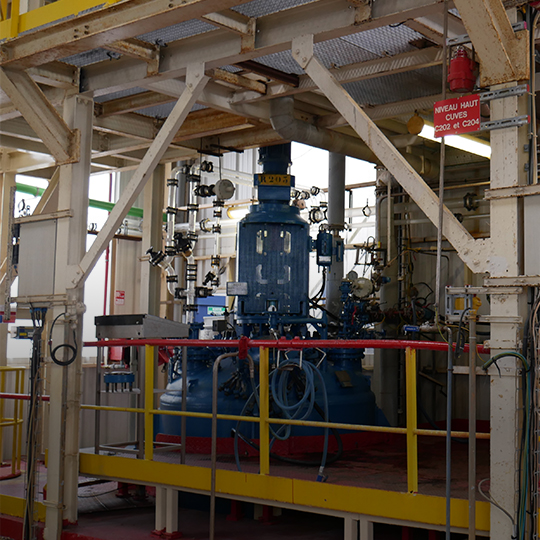
Manufacturing
Manufacturing
- Scale-up from kilograms to several tons
- Small-scale at lab
- Pilot in industrial reactors
- Pilot and manufacturing units include 70 L to 8000 L reactors
- Isolation and drying devices
- Batch process
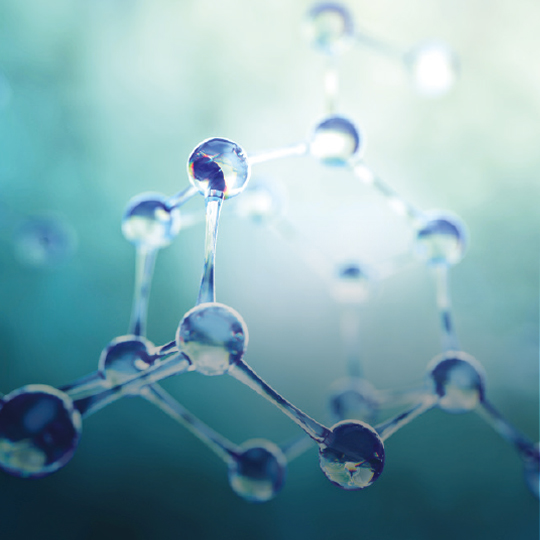
Products
Products
Producer of our own catalog
- Quinuclidines
- Bromited compounds
- Variety substituted pyridines
- Piperidines
- Chloroalkylamines
- ...
Key figures
- 160employees
- 160m3smalls molecules
manufacturing capacity - 40reactors1500 L to 8000 L
- 5buildings6th under construction
cGMP - 1000moleculesin catalogue
We guarantee our clients a completely independent, close and trusted partnership.
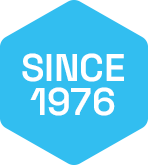